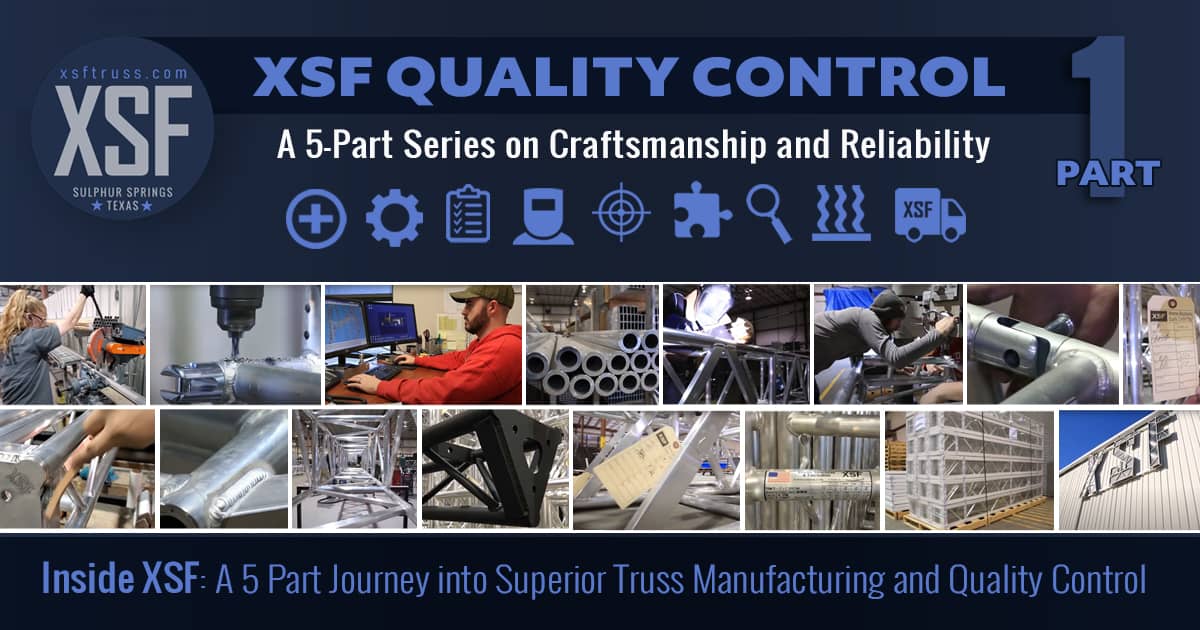
XSF has built a process that consistently meets our customers’ needs and adheres to the highest standards of reliability. This 5-part series dives deep into what makes XSF trusses reliable, durable, and crafted with care.
In this Part 1 we explore the journey, values, and meticulous steps that go into creating XSF trusses.
Precision and Pride: The XSF Manufacturing Process:

At XSF, our focus is on designing products that meet the highest expectations of performance and dependability. Located in Sulphur Springs, Texas, our manufacturing facility is where the magic happens.
Every truss is made with precision, backed by a team dedicated to excellence. From raw aluminum to the final packaging, the XSF process is designed to ensure all our products meet the highest standards.
As we go through this Series you will see that the XSF values are clear: safety, quality, and customer satisfaction. These values are a part of every step in the Quality Control Process.
Whether it’s for a concert, a custom project, or a rigging solution, the XSF process is designed to ensure customer confidence and confidence that their project will be handled professionally with expertise and care.

9 Steps of Experties & Care : XSF’s Quality Control Process
Our trusses go through a rigorous quality control process with nine key steps: Each stage is methodically planned to ensure consistent results and reliable performance. The process spans from raw material inspection to final shipment, ensuring that every truss meets both industry standards and customer expectations.
Safety and Equipment
Ensuring tools are maintained for safe and efficient production. This step minimizes risks and keeps our operations running smoothly.
Fabrication Drawings and Engineering
Turning creative ideas into reality with detailed plans and customer-approved designs. This ensures every project starts with precision and clear direction.
Raw Materials: Receiving and Inspection
Selecting the finest aluminum and inspecting it thoroughly before production begins. We ensure only top-quality materials enter our production line.
Precision Cutting and Machining Parts
Shaping and preparing materials with accuracy. Each cut is tailored to meet exact specifications for seamless assembly.
Truss Welding
Professional and Certified welding for maximum strength and reliability. Every weld is inspected to ensure structural integrity.
Final Assembly and Test Fit
Ensuring every piece fits perfectly and as designed before moving forward. This guarantees a flawless fit for all components.
Cleaning and Inspection
Conducting a final detailed and thorough check across all truss to ensure there are no defects. This step ensures every product meets our exacting standards.
Coating and Surface Finishes
Adding the finishing touches for durability and design. This enhances both the aesthetics and longevity of our trusses.
Identification, Packaging, and Shipping
Carefully labeling, packaging, and delivering every order. This step ensures your trusses arrive ready to perform.
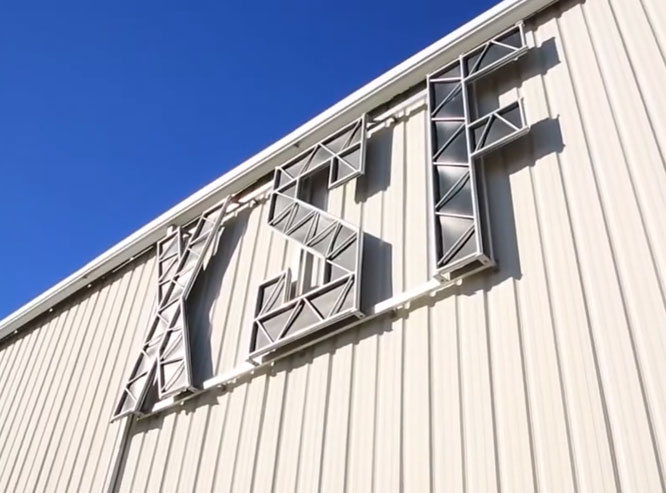
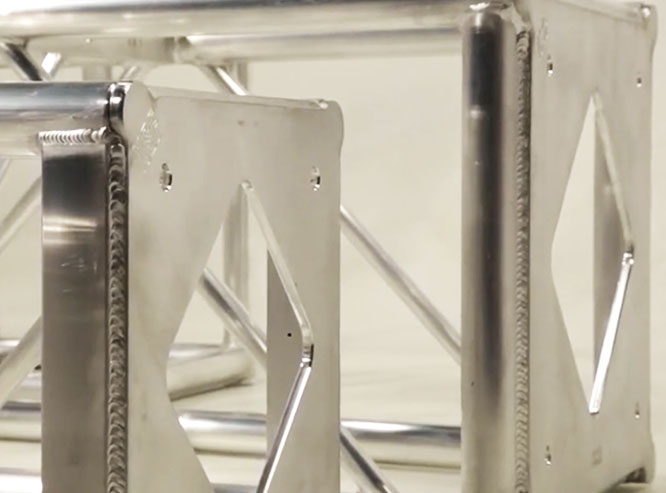

XSF Innovations & Truss Drawings Library
See how XSF is changing the Truss Industry one innovation at a time.
ConneX allows users to change truss fork-end configurations simply and within seconds. Learn more >
The Protective Bolt Plate Truss extends the life of your truss by preventing damage – Learn more >
MAV Truss is specifically designed for moving lights, audio, and video walls. – Learn more >
Visit the XSF TRUSS DRAWINGS LIBRARY
Solidworks |Â Vectorworks | AutoCad |Â DAE |Â Sketch up |Â Blender |Â Â STL
XSF Quality Control Video at YouTube
A behind-the-scenes look at our facility and offers even more insights into how XSF maintains the highest standards for its customers.